Tubes and profiles are everywhere. From vehicles and machines to furniture and buildings, there can be a multitude of tubes and profiles contained within a single structural design. Incorporating complex profiles within a design can reduce costs and enhance performance. Whatever project you work on, you don’t want to be restricted by profile cutting capabilities. This is where laser tube cutting comes to the fore.
Laser cutting is a highly adaptable technology, capable of rapid, high-quality section processing, and replacing multiple parts with a single component. A quality laser tube cutting supplier will offer a specialist profile cutting service alongside the top 5 tube and section profiles every structural designer needs at their disposal. Read the Laser Cutting Co. guide to must-have outsourced tube cutting capabilities.
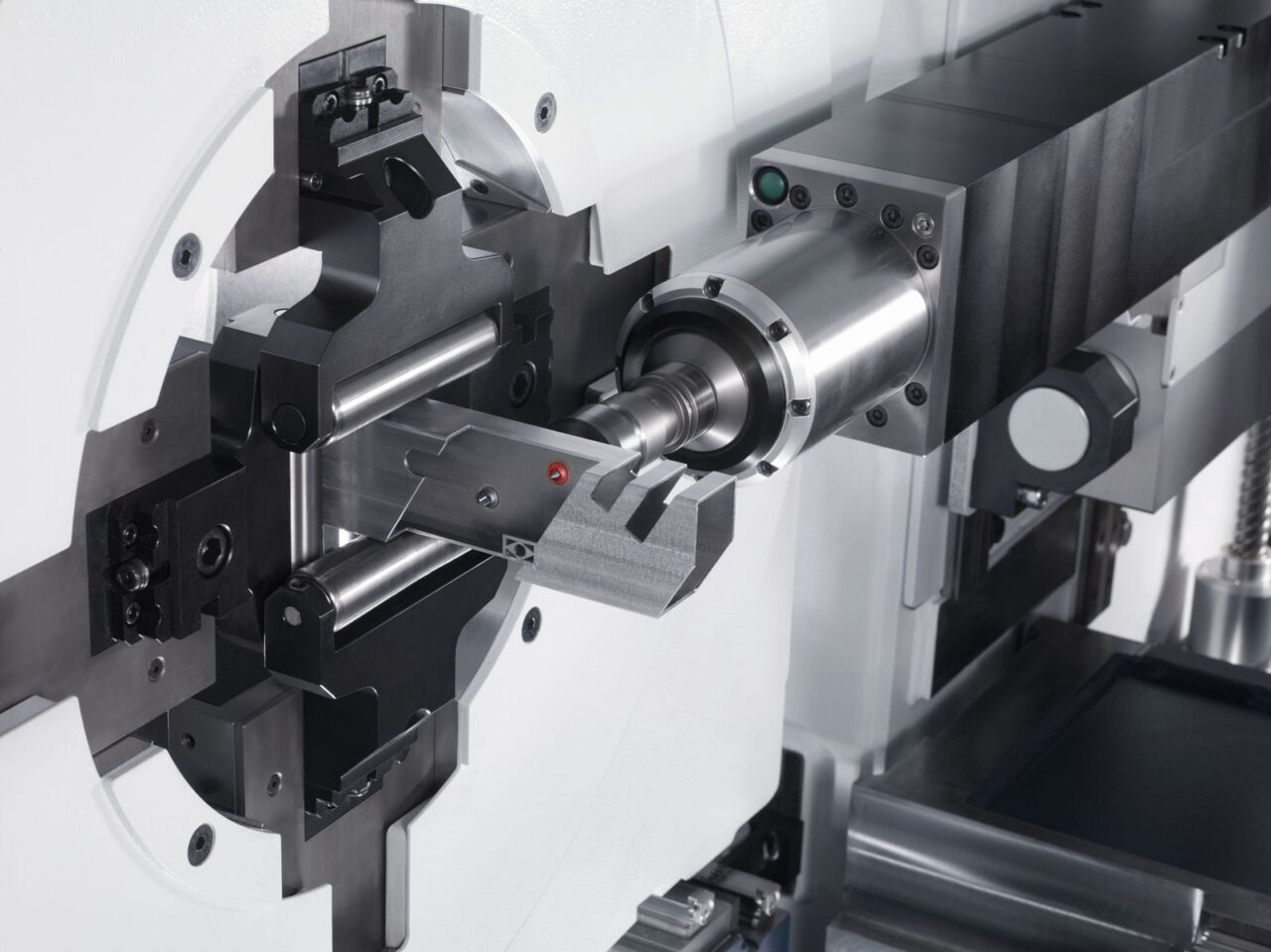
1. PFC Channel
Commonly used in construction as beams or joists, parallel flange channels, or C-sections, are strong and versatile. Whilst steel prices continue to be uncertain, and availability is expected to remain a challenge, the need to avoid over-specifying is more important than ever. Efficient design may result in a variety of flange and web thickness specifications with specialist cuts, all within a single design.
For example, a mezzanine floor designer may be faced with an intricate space in which to fit a free-standing mezz structure. Here, laser tube cutting services can deliver a range of precision mitre cuts, which fit together perfectly as they are placed over horizontal steel beams.
TLCC’s PFC channel laser cutting capability:
- Minimum 50 x 25mm
- Maximum 300 x 300mm
2. RSA Section
Rolled steel angle (RSA), or L-section steel, is a rolled structural product formed into an ‘L’ shape. Predominantly used as cleats, providing support within a larger structure, RSA sections are usually cut into many smaller sections.
Angle cleats are a tried and tested method to avoid welding. When beam sizes differ, two-sided connections can be difficult to erect. Structural designs featuring cleats, and angle cleats in particular, benefit from precision RSA section tube cutting to avoid issues on site during construction.
TLCC’s RSA section laser cutting capability:
- Minimum 25 x 25 x 3mm
- Maximum 254 x 254 x 15mm
3. Rectangular and Square Tubes
Square (SHS) and rectangular (RHS) hollow sections are commonly used as structural steel tube, such as exposed steel, trusses, and bracing elements. These are easy to join to flat sections, require minimal pre-weld edge preparation, and offer greater torsional constant than that of an open steel section. SHS is a popular mid-point between the strength of open section and the functionality and aesthetics of RHS.
Beyond the speed of turnaround, the key benefit to outsourcing square and rectangle tube cutting is the availability of multi-axis tube laser cutting. From cod mouth and bevel cuts to slots and specialist profiles, 6-axis laser tube cutting supports efficient design with lower material and construction costs. For instance, rather than joining two single parts together using four welds, laser cut a single section with a bend connection and positioning aids to do the job with just one weld.
TLCC’s square and rectangular tube laser cutting capability:
- Minimum 12 x 12mm
- Maximum 300 x 300mm
4. Round Tube and Pipe
This is where laser tube cutting really comes into its own. Dovetail, bayonet, and slot and tag connections are now a viable addition to structural designs, thanks to multi-axis laser cutting. For example, join sheet metal and round tubes with ease, by incorporating tube-blank connections within your design.
Where once multiple parts might have been required to complete an assembly, laser tube cutting can achieve the same result using a single part. Over the course of a project, the economies of scale are impressive, particularly in the context of large stainless steel projects such as balustrading.
TLCC’s pipe and round tube laser cutting capability:
- Minimum 12mm Ø
- Maximum 406mm Ø
5. Universal Beams
The backbone of commercial and industrial buildings, universal beams, also known as ‘I’ or ‘H’ beams, distribute weight evenly and are widely used for their ability to bear enormous loads. For steel fabricators, the impressively clean finish achieved by laser tube cutting reduces weld preparation requirements. Over the course of a job, this can significantly boost productivity.
Laser tube cutting speed combined with automated processing, results in a significant cost reduction. Moreover, the greater the volume of universal beams to be cut, the lower the processing cost per profile.
TLCC’s universal beam laser cutting capability:
- Minimum 127 x 76mm (13kg)
- Maximum 254 x 146mm (43kg)
Perfect Coordination
Perfectly coordinated components, both low- and high-volume, are a game-changer for structural designers. Laser tube cutting massively reduces welding requirements and the need for additional fittings. Laser cut self-jigs and part folds achieve an accuracy of +/- 0.25mm. The possibility to achieve complex connections with less material and less intervention reduces project costs by up to 50%.
Rather than replacing that ageing mitre saw and maintaining a stock of machine tools, outsource tube and profile cutting. Benefit from the expertise and cutting technology investments of a reliable partner.
From material to completed part in just one process, ready for assembly as per drawing requirements, The Laser Cutting Co. can reduce manufacturing processes by up to 50%.