The 21st century has witnessed the rapid progression of smart technology, analytic intelligence, automation and a plethora of indispensable advancements at the fingertips of businesses and clients globally. As the digital age has evolved, the demand for adept services continues to increase as the fourth industrial revolution, also known as Industry 4.0, transforms innovation now and continuously in the future.
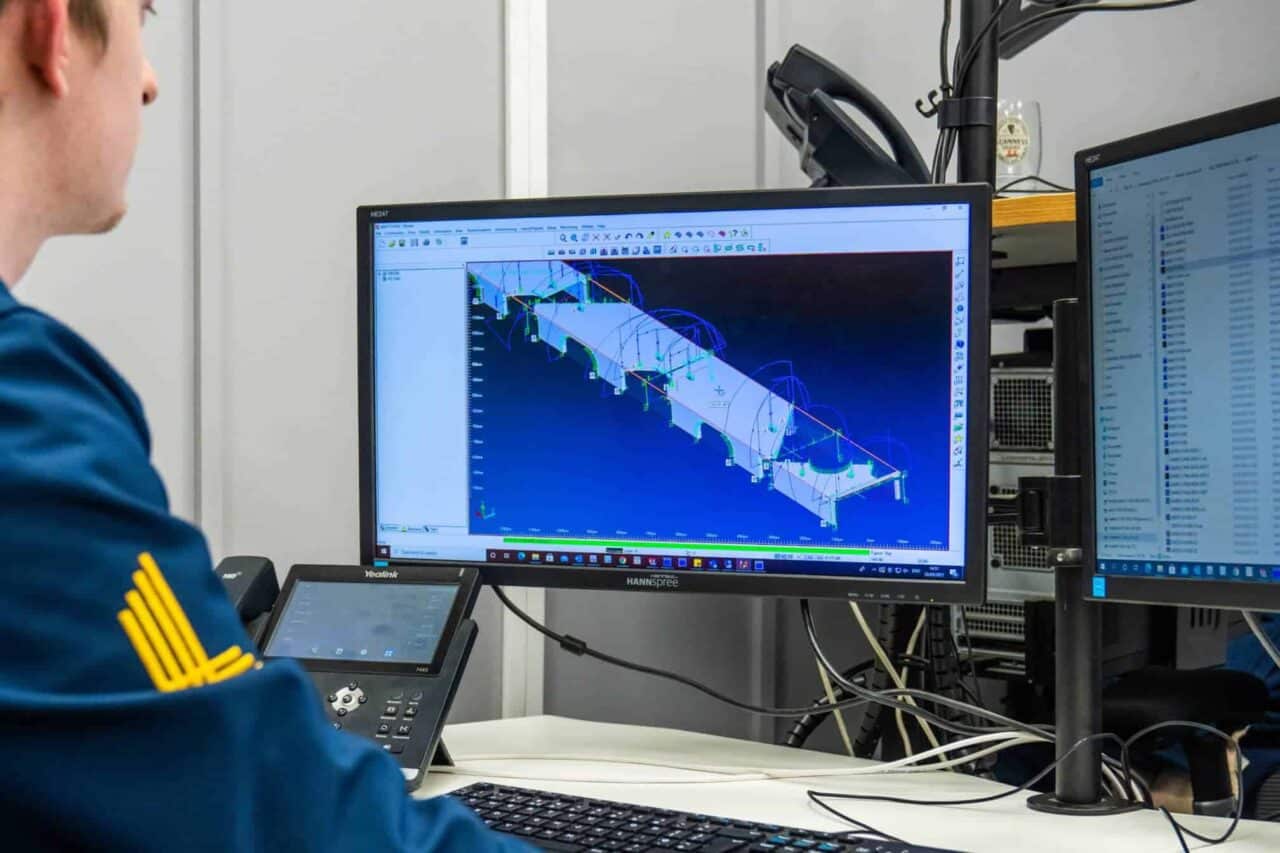
The Fundamentals of the Fourth Industrial Revolution
The fourth industrial revolution rose to prominence within the mid-2010s and propelled digital transformation off the back of the first computers. Currently, the scope of potential is endless, and modern manufacturing is riding the crest of disruptive technologies. There are four key fundamentals that have been adopted within Industry 4.0, all of which apply across varying sectors.
- Connectivity: Sensors, Internet of Things (IoT), cloud technology, blockchain
- Analytics and intelligence: Advanced analytics, machine learning, artificial intelligence (AI)
- Human-machine interaction: Virtual and augmented reality (AR/VR), robotics and automation
- Advanced engineering: Additive manufacturing, renewable energy, nanoparticles
The Growing Development of Laser Cutting in Industry 4.0
Laser cutting technology is constantly evolving, offering seamless and rapid results for complex processes across a spectrum of applications. Most notably, laser cutting has dominated sectors such as aerospace, automotive, metal profiling and fabrication to offer stellar results within fine tolerances. Considering the key fundamentals of the fourth industrial revolution, there have already been great strides in laser cutting technology, with new systems becoming adopted within production processes on a frequent basis.
Intelligent Robotics and Automation
Automation has been prevalent in laser cutting machines since the 1980s, as the brains behind the equipment, naturally it starts to evolve. The introduction of AI (Artificial Intelligence) technology has cemented itself as the forefront of laser cutting systems, enhancing automation and intelligent decision-making capabilities. Adaptive AI is capable of automating laser cutting of varying materials, calculating complex paths and depths that mitigate human error and guarantee exceptional consistency on even the most volatile materials. With machine learning technologies, AI continues to evolve and tackle rising challenges in production, handling new materials and designs with minimal input.
Due to the integration of automated technologies, production lines can operate 24/7 without disruption in operations. Utilising advancements such as automatic loading and unloading systems eliminates the potential risk of error and bloated processing times.
Emerging Technology
IoT software has become standardised within digital technology, transmitting signals across networks and cloud platforms to aid data collection and machine status during operation. This integral real-time data provides insights into the operational performance of machines from onsite and remote locations. This is especially beneficial for monitoring system maintenance, preventing equipment failure beforehand and backing up valuable analytics. Rather than work as independent machines, laser cutting equipment can be part of a cohesive system and work collectively as one from existing data sets. Modern technology now has the scope to handle larger and more complex designs, offering flexibility to efficiently cut bespoke requirements across various quantities.
Responsible Sustainability
The fourth industrial revolution generates an insightful conversation about manufacturing processes and the future of sustainable practices. The introduction of intelligent systems weaved amongst existing processes goes on to promise dynamic laser cutting functionality, working in tandem to optimise efficiency and reduce material waste.
Renewable energy sources, along with robotics, significantly help to eliminate harmful pollutants and head towards net-zero initiatives. Accompanied by digital twin software, which can simulate material performance under various processes in metal profiling production, can also further reduce waste by targeting problems before they arise.
Shifting Work Culture
In Industry 4.0, below the surface of intelligent software and equipment, is a simmering conversation about how the workplace culture can be sufficiently optimised. There is great demand for the workforce to offer opportunities that upskill and reskill employees to ensure they retain the essential knowledge required for their roles. As the tide of technology shifts and changes direction, so do the expectations from governing bodies for businesses to train their staff and become adaptable to new processes. It is therefore beneficial for companies to invest in the personal development of individuals, not only to uphold morale but retain a customer base that can see quality reflected in their final product.
The fourth industrial revolution has altered the face of manufacturing altogether, and it’s becoming a greater necessity for manufacturers and suppliers to instil these adaptive processes at their foundation to remain competitive in saturated markets. With the fifth industrial revolution emerging on the horizon, encouraging the harmony between humans and machines, there is now greater demand from customers who expect more from varying sectors and diverse skill sets that can maintain the integrity of operations.
The Laser Cutting Co.’s Commitment to Innovation
Since the conception of The Laser Cutting Co. in 1981, the drive towards innovative technology and pioneering sustainable practices has been the backbone of our services. We continuously invest in the latest technology, offering smart design production and intelligent software that increases downstream efficiency and eliminates customer rejects with a 50% cut in production time.
As part of our eco-conscious initiatives, we have installed over 1,300 solar panels and a fleet of electric forklifts across The Laser Cutting Co. and our sister site, Charles Day Steels. Due to our consistent journey towards green manufacturing, we are proud to achieve ISO 14001 certification which rewards businesses for their ongoing commitment. Every aspect of our operations aims to deliver economical and precise results without compromising environmental factors.
Our expert engineers can assist with all aspects of your project, from sourcing material type, thickness, bespoke patterns and project complexity. For further guidance on your personalised project requirements, contact a member of our team today.