In metal fabrication, precision is paramount. While there is more than one way to skin a cat, the need to produce ever more complex cuts, fine contouring, and optimised nesting, presents a quandary for metal fabricators. Weighing up time and cost implications of in-house or outsourced metal cutting, there are several considerations to find the optimum solution for complex fabrication projects. In this fabricators guide, we explore why outsourced laser cut sheet metal is a winning solution.
Laser cutting has been around since the 1960’s with fibre lasers available for commercial use during the 1980’s. Fibre lasers are now applied to a variety of applications, including marking for traceability and security, sensors, cutting, welding, and additive manufacturing techniques. The adoption of fibre lasers is a result of the technology’s precise beam control. Fibre laser cut sheet metal is a recent addition to the metal cutting industry, having appeared on the market in 2009.
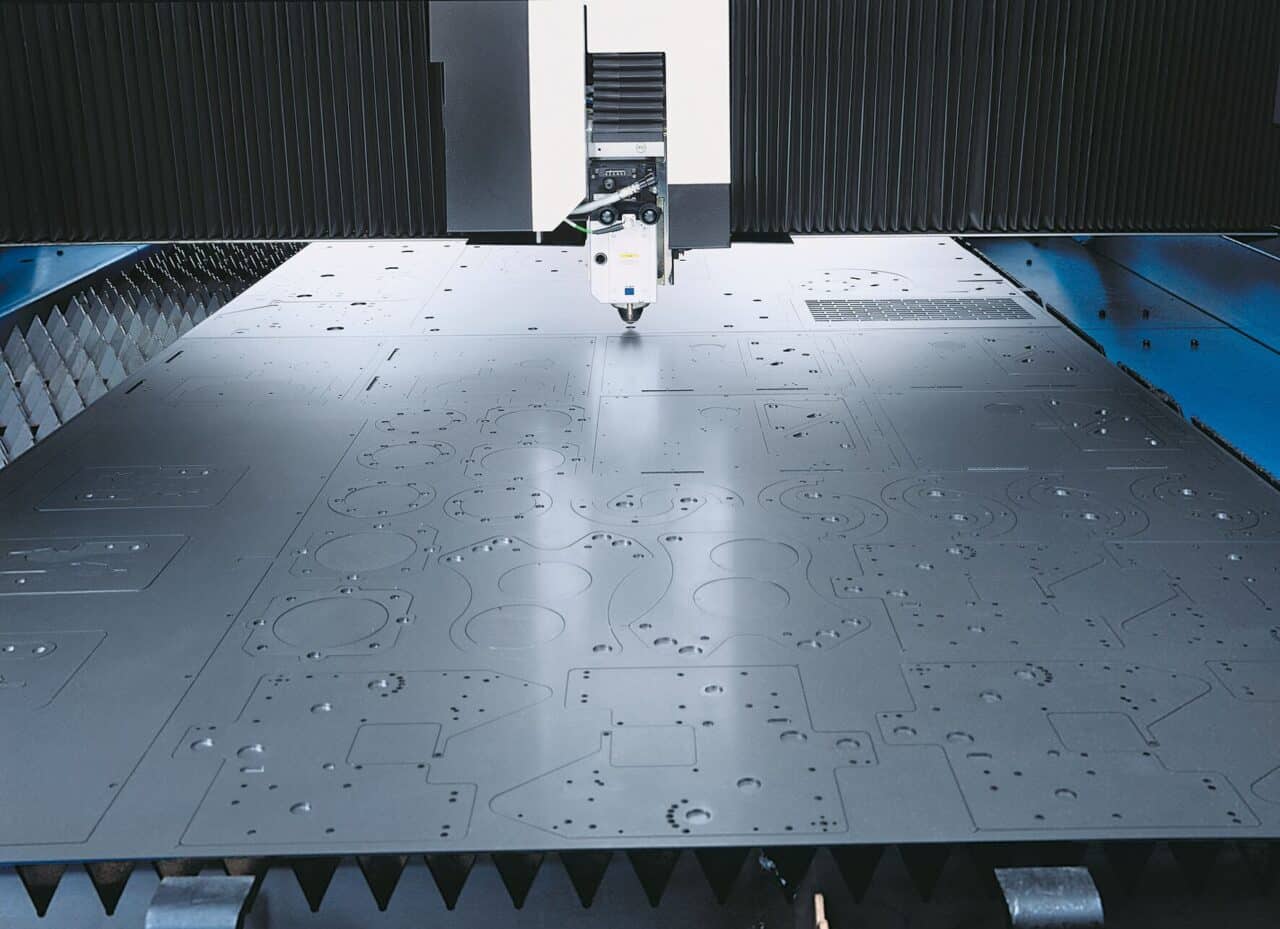
The Cost of Complexity
For metal fabricators and associated OEMs, the complexity of metal profiling is a growing challenge. Developing technology is fuelling the race towards ever more complex cuts and increasing high-quality finishes. The advent of fibre lasers has significantly raised the bar in the metal profiling industry.
Fibre lasers are a solid state cutting technology, able to cut faster than mechanical and even CO2 laser cutting technologies. However, it’s not always about who can cut fastest. Fibre laser cut sheet metal has a +-0.25mm cutting tolerance, offering the level of precision designers and downstream engineers demand. Furthermore, as a contact-free sheet metal laser cutting technology, fibre lasers present almost no risk in terms of part damage, compared to mechanical metal cutting.
Quality cuts reduce downstream intervention. Precision means both tighter nesting and easier-to-release parts from the (minimal) scrap skeleton. Not only is waste reduced, but productivity and yield are increased during the assembly process.
Time and Money
Fabricators tend to use a set of mechanical cutting tools. Bandsaws, guillotines, and slitting machines are a low-cost investment initially but significantly add to sheet metal processing times. Working with a range of materials and thicknesses increases set up time and usually requires a greater range of tooling for each process. For this reason, many fabricators and OEMs outsource metal profiling to a trusted sub-contract laser cutting service.
The versatility of laser cut sheet metal is hard to beat. A single laser can cut, slot, slit, and contour with little to no post-processing required. Burr-free with easy-to-remove parts makes a strong case for laser cutting sheet metal. Lasers incorporates both cutting and finishing in one, whereas mechanical cutting requires several processes to achieve a similar result.
There are significant cost savings to be derived from outsourcing metal profiling:
- Less machinery to maintain
- Fewer processes to achieve quality cuts
- Reduced downstream intervention
- Lower onsite power consumption
- Less part damage during cutting and removal.
- Accurate and reliable parts on demand.
The Finishing Touches
Chamfers, bevels and countersinks are usually achieved with specialist machinery and tools, most of which are standard equipment in a fabricators workshop. An essential stage of the finishing process, sheet metal finishing tools prepare a finished product ready for assembly. Essential but laborious, requiring further investment in specialist equipment and skilled labour – currently in short supply.
Laser cut sheet metal incorporates finishing into the cutting process. A laser can access those hard-to-reach areas, increasing finish quality and reducing the risk of injury. Fibre lasers vaporise material using a hyper-focused beam, resulting in a high-quality finish.
Outsource to Keep Pace
Fibre lasers are changing the face of metal fabrication. Finer results are achieved faster, in a single pass, using just one machine. Fibre laser cut sheet metal, and tube and section metal, are superior products compared to mechanically cut metal. For fabricators, the competitive edge lies in fibre laser technology.
Do you invest in fibre laser technology or find a laser cutting company to outsource sheet metal cutting? The pace at which cutting technologies are developing makes a clear case for outsourcing metal profiling. If a reliable sub-contract laser cutting service can be found, fabricators will reap greater long term benefits from the continued cutting technology investments of a third party. In the short-term, outsourcing avoids the need to finance investments in advanced cutting technologies, such as a fibre laser cutting machine, Long-term, outsourcing provides fabricators with access to burgeoning technologies and keeping ahead of competitors trying to manage every cutting and finishing process in house.